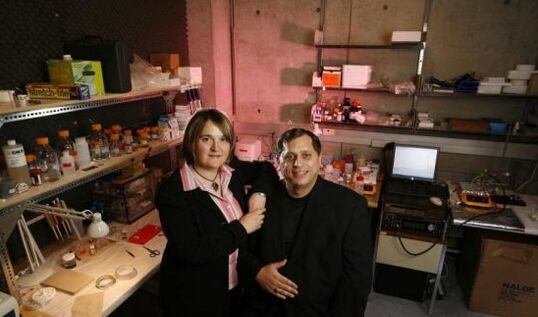
Mihri and Cengiz Ozkan, two researchers at the Burns School of Engineering at the University of California, Riverside.
This article refers to the address: http://
Beijing time on June 19th news, according to foreign media reports, the University of California, Riverside, Burns Institute of Engineering researchers recently developed a three-dimensional integrated structure of tapered carbon nanotubes decorated with silicon materials for lithium-ion batteries Above the electrodes, this structure can reduce the charging time of portable electronic devices from hours to ten minutes.
A lithium ion battery is a rechargeable battery used on portable electronic devices or electric vehicles. However, there are still some problems with this battery. The weight of batteries carried by electric vehicles often accounts for a large proportion of the weight of the entire vehicle, and the size of the batteries on portable electronic devices is difficult to further reduce. Silicon is a high-quality electrode material, which has attracted more people's attention because the total charge capacity of this material is more than 10 times higher than that of commercial graphite-based lithium-ion battery electrodes. If a silicon material electrode is used instead of a conventional graphite electrode, the total battery capacity may be increased by about 63%, and the battery size will be smaller and the weight will be about 40% lighter.
Researchers at the University of California, Riverside, Burns School of Engineering recently published the latest research results in the magazine "Small", detailing the three-dimensional integrated structure of the silicon material decorative tapered carbon nanotubes of the lithium ion battery electrode, and the structure Development process such as chemical vapor deposition and inductively coupled plasma treatment. Lithium-ion batteries based on this novel structure have been tested to have high reversible capacity and good cycle stability, and this structure exhibits excellent electrical stability and irreversibility even at higher charge and discharge rates. The charging speed is almost 16 times faster than the traditional graphite electrode.
The researchers believe that there are two main reasons why the structure of the electrode charging and discharging speed is too fast. The first reason is that the seamless connection of copper-covered graphene to carbon nanotubes enhances the activity of the material and promotes the charging process and heat transfer in the electrode system. The second reason is that the tapered structure provides a breakthrough channel for the electrolyte to quickly enter the electrode, which improves charging efficiency and performance.
With the development and progress of domestic industry, machining has changed a lot, Precision Machining technology has come to the fore, many industries such as household appliances, automobiles, hardware and medical manufacturing products more or less use precision parts. It may be just a component, or it may be a core component in a mechanical device. In a word, it is very important and plays an irreplaceable role.
And these precision parts for precision machining manufacturing there are two processes, one is hot processing and one is cold processing, hot processing is through heat treatment and other ways to make parts in very warm conditions under the biochemical or physical changes to achieve the shape change requirements. And cold processing is at room temperature without chemical and physical changes to achieve shape changes, generally using cutting technology. In the future, on the premise of meeting processing and environmental protection, precision machining will be combined with science and technology to become an important and sustainable science.
Precision Cnc Machining,Cnc Machining Parts,Custom Cnc Machining,Precision Cnc Turning Parts
Tianhui Machine Co.,Ltd , https://www.thcastings.com